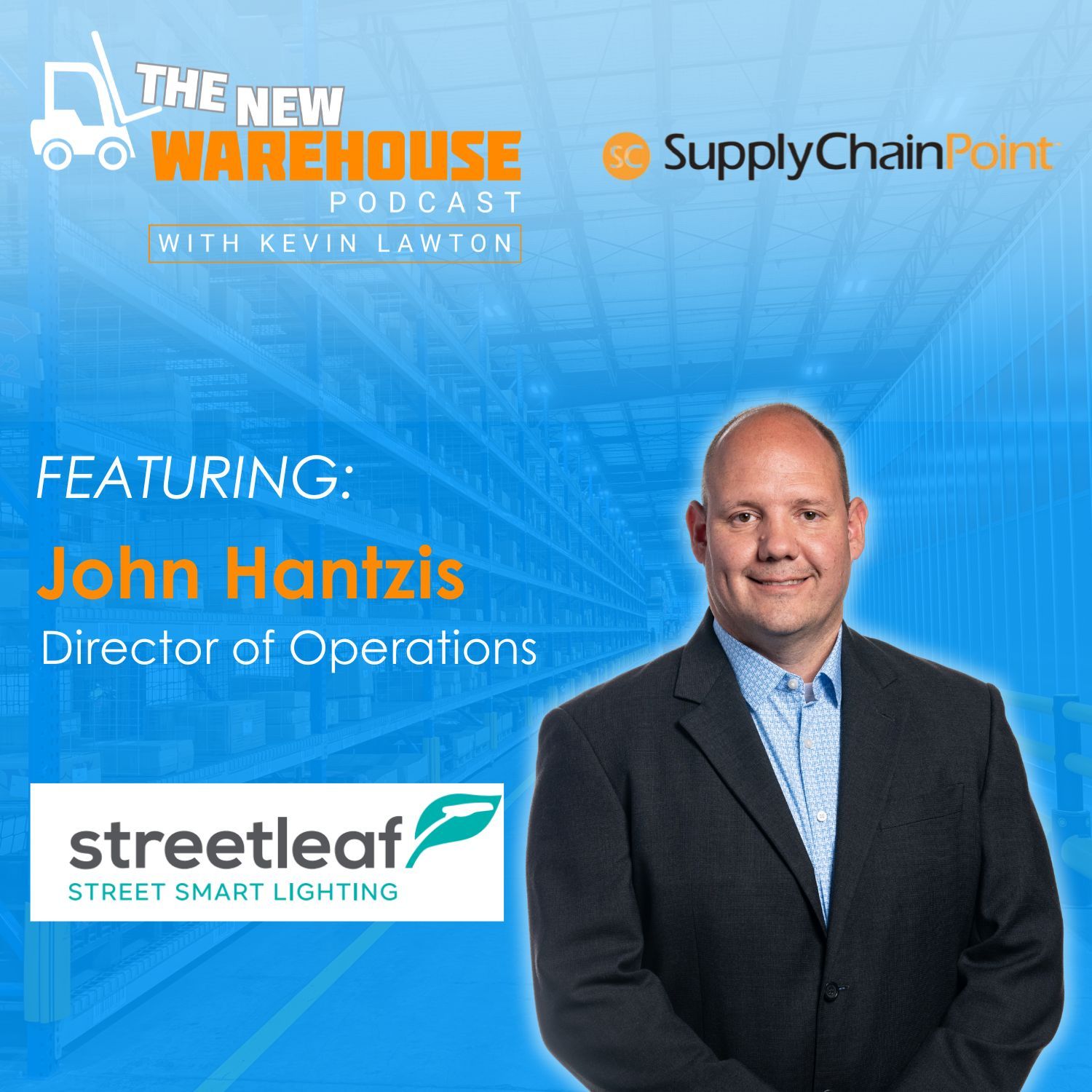
Supply Chain Point: Shining a Light on Supply Chain Theft with Streetleaf
In this episode of The New Warehouse Podcast, Kevin chats with John Hantzis, Head of Operations at Streetleaf and Transportation Sector Chief for InfraGard. Streetleaf is a solar street lighting company recognized for its rapid deployment systems and storm-resilient infrastructure, primarily serving master-planned communities.
John shares how Streetleaf developed a lean and adaptive warehouse strategy, built to withstand tariff volatility and unpredictable demand. He also delves into his role with InfraGard, where he collaborates with the FBI to enhance cybersecurity in transportation. From strengthening internal operations to detecting low-tech theft, John offers a unique dual perspective that blends real-world operations with national security insights.
A Lean but Resilient Approach to Distribution
Streetleaf operates its warehouse in Zephyrhills, Florida, handling both imported and manufactured components. According to John, they’ve built in overflow flexibility to stay ahead of demand shifts and political uncertainty. “We used the 3PL space to kind of handle some of that overflow for us to be able to react more quickly for our customers in need,” he explains.
Their core equipment, solar panels, lightheads, and aluminum poles, requires a mix of indoor and outdoor storage, which complicates 3PL selection. To manage this, they plan for scenarios such as port strikes and tariff spikes by proactively bringing in inventory. But demand planning remains a challenge. “You have the customer that you are expecting to order a certain amount, and that is either much higher or significantly lower,” John notes. This forces a constant balance between overstocking and stockouts, while keeping customer responsiveness high and carrying costs in check.
Breaking Down Operational Silos
As the industry evolves, John believes that many companies continue to struggle with fragmented systems and unclear objectives. “Distribution, warehousing, 3PL is still siloed,” he explains. Departments such as accounting, IT, and sales often operate with conflicting KPIs, making collaboration challenging. To address this, he emphasizes the importance of stakeholder buy-in. “You need to have full buy-in by all your departments,” he says.
Each function requires clarity on its role in implementing a new tool or process, whether it involves evaluating cost structures, managing vendor integration, or enhancing sales enablement. John advocates for a practical approach: start with the outcome and reverse-engineer the process with every department at the table. “You need to be looking at the magnifying glass knowing that far-reaching goal is there, but you gotta focus on the now,” he says. In his view, operations and sales don’t have to be at odds—alignment can increase both performance and customer satisfaction.
Inside the War on Supply Chain Theft
In his role with InfraGard, John partners with the FBI and local businesses to identify and combat both cyber and physical threats to the transportation sector. Surprisingly, many security breaches are not sophisticated. “A lot of times people think it’s high tech that’s beating them—it’s actually low tech,” he reveals. Most thieves can open a trailer in under 15 minutes without disturbing the security seal.
Criminals target electronics and perishables, which are easy to offload and hard to trace. “If they’re able to recover a box…they have no idea—is that one missing? Is it stolen? Is it legitimate?” he explains. To prevent this, he recommends layered strategies: vetting every MC number and license, using GPS and RFID tracking, and installing solutions to alert you the moment a trailer opens. “There’s even companies out there that have a little cable that fits through the security seal but also goes inside the trailer with light sensitivity,” John says. These systems can help lower insurance premiums and reduce theft payouts. His bottom line: the sooner you detect tampering, the more likely you are to stop it.
Key Takeaways on Supply Chain Theft
- Streetleaf’s hybrid warehouse and 3PL strategy offers flexibility in response to political, seasonal, and customer-driven disruptions.
- Complete departmental alignment is crucial when integrating new tools or workflows.
- Many companies still operate in silos with misaligned KPIs, which reduces overall efficiency.
- Most cargo theft is low-tech, often executed without breaking the security seal.
- Vetting truckers and equipment, tracking routes, and using light-sensitive seals can prevent theft and lower insurance premiums.
- Solutions like Genlogs can identify bad actors before goods leave the dock.
Listen to the episode below and leave your thoughts in the comments.
Guest Information
For more information on Streetleaf, click here.
To connect with John on LinkedIn, click here.
For more information about supply chain theft, check out the podcasts below.
510: Addressing Lost and Stolen Packages with Deliverlitics
582: Maximizing Value with Operational Consulting with Supply Chain Alliance