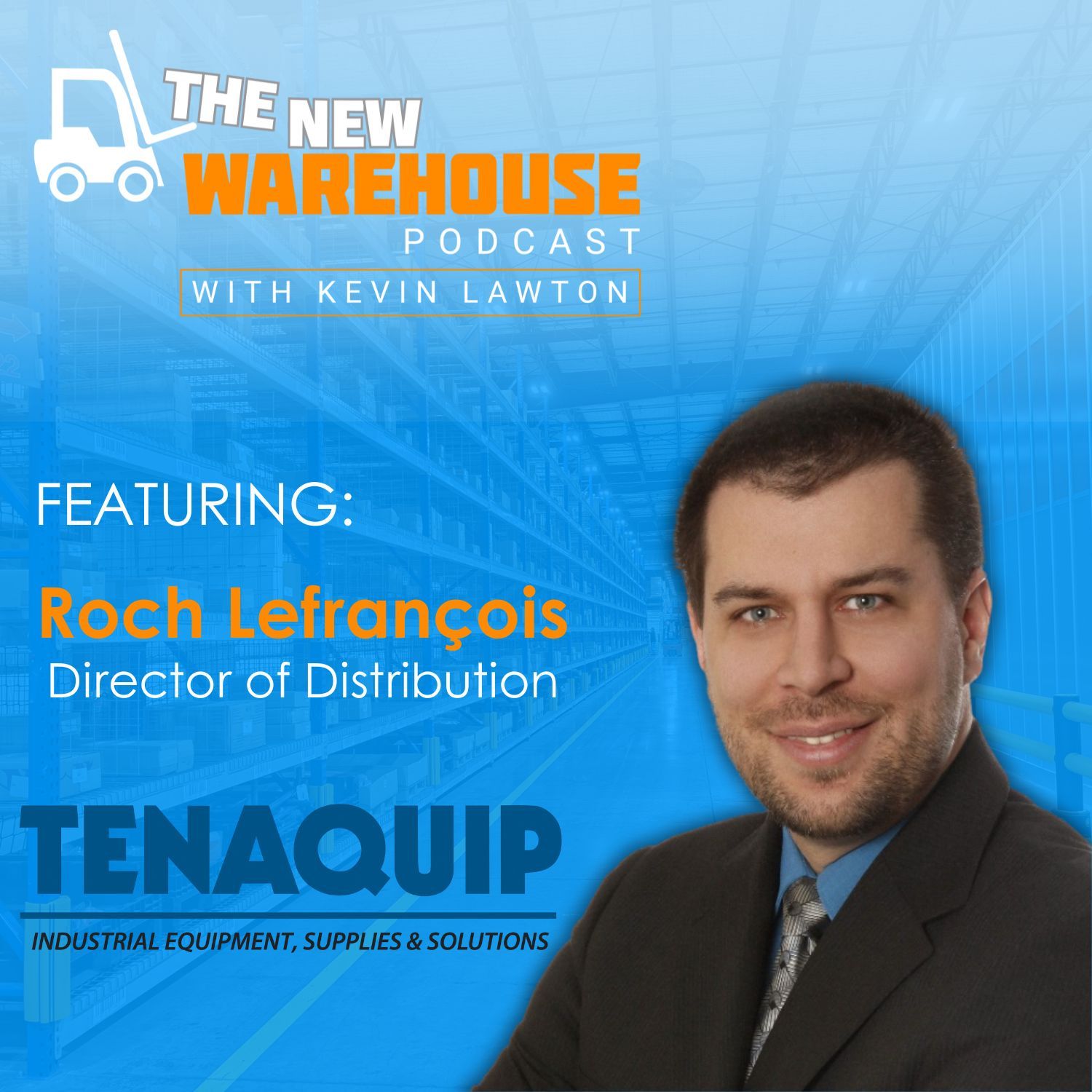
586: Distribution, Automation, and the Human Element with Tenaquip
In this episode of The New Warehouse Podcast, Kevin chats with Roch LeFrancois, Director of Distribution at Tenaquip, a Canadian industrial supply distributor known for its wide-ranging catalog and focus on customer service. Roch shares how his passion for technology and operations has shaped his leadership journey across grocery, pharma, real estate, and distribution. With over 180,000 SKUs, automation challenges, and sky-high customer expectations, he emphasizes the importance of adaptability, balance, and keeping the human element central to every process.
Automating for Complexity, Not for Show
Tenaquip maintains 55,000–60,000 SKUs in stock at all times, ranging from nuts and bolts to step ladders. That complexity drives Roch’s passion for automation—but not at the expense of flexibility. “If the solution is more work, it’s probably not a good solution,” he says. He favors hybrid systems with redundancy and fallback options, like conveyors or pick-to-light systems, over high-risk ASRS environments with limited access during breakdowns.
“Some solutions are very efficient—until they fail,” he explains. “If your ASRS goes down, that could be thousands of pallets you can’t access.” AI, however, excites him for its potential to optimize slotting and storage intelligently, without increasing risk. “AI will bring automation to another level in terms of productivity.”
Distribution Expectations and the COVID-19 Wake-Up Call
COVID-19 permanently raised the bar in distribution. According to Roch, “We had to get better because Covid increased that volume for everybody.” The pandemic accelerated automation adoption and forced companies to rethink scheduling, capacity, and inventory positioning.
But today’s biggest challenge isn’t infrastructure—it’s customer expectation. “People expect next-day delivery by default now,” Roch says. “There’s no room for error anymore, and you have to be efficient every time.” That pressure is reshaping warehousing norms across Canada and beyond.
At the same time, Roch credits the crisis with creating a culture of innovation. “COVID helped the distribution network here. It made people more resilient and more creative.”
Culture, Interviews, and Hiring for Fit
Beyond tech, Roch brings an intensely human lens to leadership. He sees warehouse work as something that “can improve people’s lives for 20 or 30 years” through thoughtful process design and supportive environments. That’s why he’s hands-on with hiring, training, and team engagement.
“I don’t use a script in interviews. I just have a conversation. But I know the job I’m hiring for.” He looks for attitude and cultural fit over credentials, adding: “Even if they’re productive, if they don’t fit the team, it can be toxic.”
Roch also stresses the value of transparency and walkthroughs during the interview process. “Show them the workplace. Let them see what they’re actually signing up for.” His advice for fellow managers? Know the job yourself, listen to your team, and remember that they see the things you’ll miss.
Key Takeaways
- Automation Decisions Are Grounded in Practicality – Roch emphasizes the importance of redundancy and warns against overreliance on high-risk systems like ASRS.
- AI Seen as a Game-Changer for Slotting – Rather than replacing people, Roch sees AI optimizing how and where inventory is stored for smarter throughput.
- Customer Expectations Drive Operational Standards – With next-day delivery now the norm, Tenaquip builds its processes around speed and zero-margin-for-error performance.
- Crisis Sparked Long-Term Innovation – The pandemic forced new thinking and accelerated warehouse improvements from which Tenaquip continues to benefit.
- Hiring Focuses on Fit and Transparency – Roch doesn’t use scripts in interviews, prefers informal conversations, and ensures candidates know the work environment before signing on.
Listen to the episode below and leave your thoughts in the comments.
Guest Information
For more information on Tenaquip, click here.
To connect with Roch on LinkedIn, click here.
For more information about warehouse distribution, check out the podcasts below.
585: Holman Logistics on Longevity, Loyalty, and a People-First Approach
543: Toyota Material Handling’s Next-Gen Distribution Center
417: Flexible Solutions for Warehousing, Fulfillment, and Distribution with Flexe