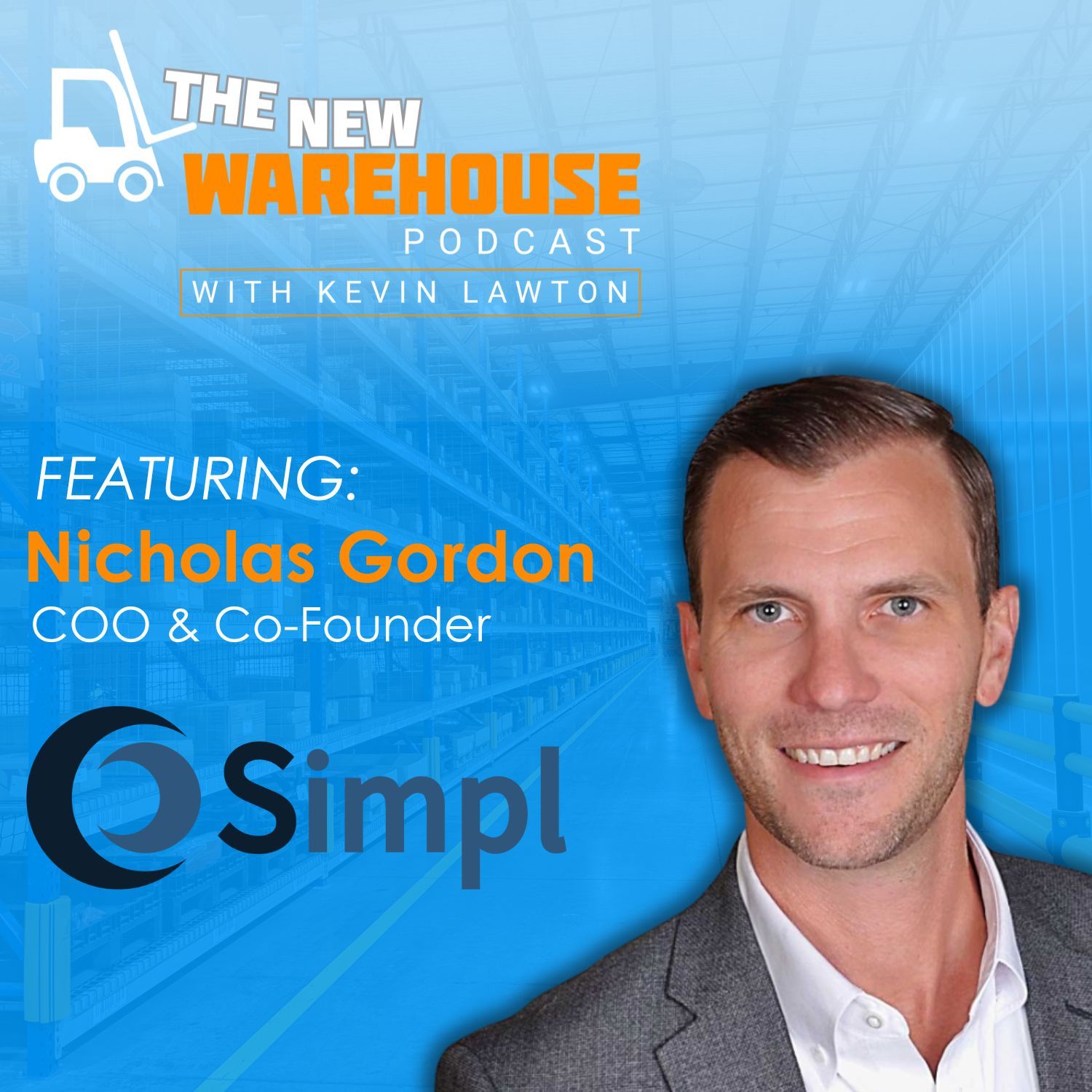
604: A SIMPL Solution for Automating Warehouses
In this episode of The New Warehouse Podcast, Kevin chats with Nicholas Gordon, Co-founder and COO of SIMPL Automation, a company redefining ASRS (Automated Storage and Retrieval Systems) deployment. Instead of tearing out infrastructure to make way for automation, SIMPL delivers an adaptive solution that installs directly onto existing racking, cutting down on cost, disruption, and environmental waste.
With 15 years of integration experience under his belt, Nicholas brings a holistic view of the market and shares how SIMPL’s solution emerged from observing one consistent pain point: warehouse automation upgrades are too invasive, and too much steel ends up in the dumpster.
The ASRS Market Is Evolving—Not Revolting
Automation vendors are flooding the market, but Nicholas believes what we’re seeing isn’t a revolution—it’s refinement. “Right now I feel as if we’re in kind of this evolutionary state where small changes are being made… making slightly better offerings on a day-to-day basis,” he explains.
This movement isn’t necessarily a bad thing. For warehouse leaders whose careers can rise or fall based on a $10–50 million automation investment, incremental improvements offer a safer path forward. But the sheer volume of options at shows like ProMat 2025, with sometimes 40 or 50 ASRS vendors, can create more confusion than clarity. According to Nicholas, “Nobody’s done a great job of addressing the long tail of brownfield facilities.”
That’s where SIMPL enters the conversation, carving out space by going after the majority of warehouses that aren’t built from scratch. “If you look across North America right now… the large majority of facilities are 15, 20, 30 years old.” Instead of pushing those operations toward disruptive overhauls, SIMPL makes automating warehouses accessible by working with what already exists.
Automating Warehouses with Existing Infrastructure
SIMPL’s core technology installs on existing racking—regardless of whether it’s structural, roll form, pallet, or case. “We’re able to go on what you have… and our intent is to try and bring in that density and labor play… on that existing racking,” Nicholas explains.
This approach not only lowers upfront investment but also avoids the soft costs overlooked in greenfield projects. “Most customers are pretty good at handling the direct costs… where I think some folks struggle is the more soft costs associated with jobs that are highly disruptive,” he notes. Those disruptions could include rerouting fulfillment to another node, flexing labor across sites, or leasing extra space. All of which have operational consequences.
For some customers, SIMPL repositions racking to increase density, but it never requires a complete teardown. “We’re not going to pay for the cost of new rack, we’re just going to pay for the installation cost,” Nicholas adds. Whether a customer chooses to relocate racks or leave them untouched, SIMPL’s goal is to eliminate the high-friction decisions that typically accompany retrofits. “We’re attaching ourselves right to the face of the rack. We’re not making any modifications to it.”
Simpler Bots, Smarter Operations
A standout aspect of SIMPL’s adaptive system is its use of two specialized robots: one for vertical movement along the rack and one for ground transport. Nicholas is clear about the rationale: “I like my robots to essentially be specialists.”
He argues that generalist robots often lead to higher costs and complexity. “That drives reliability, availability… drives down spare parts, costs, drives down preventive maintenance costs,” he explains. Their system minimizes moving parts by simplifying robot responsibilities, making long-term ownership less expensive and easier to manage.
The current setup handles totes and some limited case sizes, but Nicholas hinted at what’s next: “We’ve got some stuff on the horizon… that will allow us to take on a much deeper variation in case sizes.” While he kept specifics under wraps, it’s clear SIMPL is preparing to move beyond containerized storage and into more flexible case-handling applications.
And in terms of industry buzz, he’s still cautious about humanoids. “I think we’re pretty far away from a dark warehouse… It’s pretty expensive to be an early adopter of a revolutionary technology.” For now, SIMPL’s focus remains squarely on practical, immediate impact, not hype.
Key Takeaways on Automating Warehouses
- SIMPL installs directly onto existing racking, whether structural, roll form, pallet, or case, and requires no infrastructure teardown.
- Leverages two specialized robots for greater simplicity, lower costs, and higher system availability
- Minimizes soft costs and supply chain disruptions that often go uncalculated in retrofit projects
- Works across greenfield and brownfield sites, enabling scalable, network-wide deployment
- Designed for warehouse operators prioritizing density and labor efficiency without upending operations
Listen to the episode below and leave your thoughts in the comments.
Guest Information
Connect: Nicholas Gordon on LinkedIn
For more information about automating warehouses, check out the podcasts below.
601: Warehouse Automation Readiness with SLAM
597: Making Warehouse Automation More Accessible with iAutomate